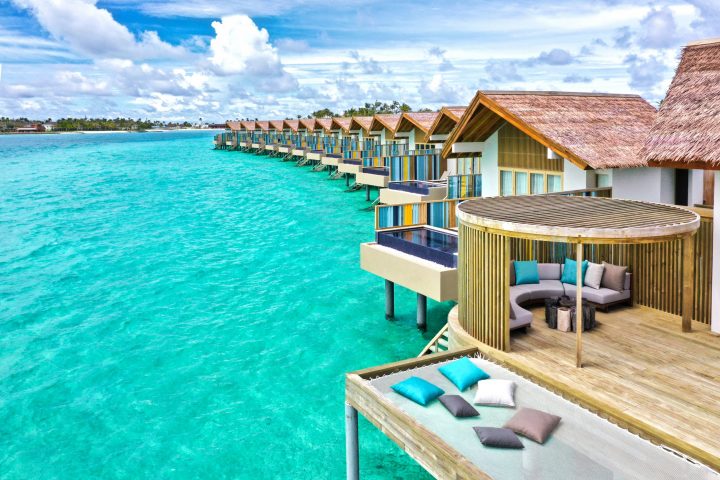
Development of Emboodoo Lagoon, AIMA Construction’s Landmark Project
For the 100% Maldivian owned and family operated business, AIMA Construction Pvt Ltd, winning the Crossroads Project at Emboodhoo Lagoon was a catalyst for change on an unprecedented scale. AIMA Construction moved mountains in completing the project that grew from one package to three packages, valued at USD 80 million, within a remarkable 16-month timeframe – which is no mean feat by any standards.
AIMA Construction was initially contracted to do the Back of House and MRP buildings, which was a project worth USD 24.1 million within a tight deadline of 8 months. However, after their client Dreamlands Development Pvt Ltd, on behalf of Singha Estates, observed the speed and skilled workmanship being undertaken at the site, the company was awarded with two new projects to complete: the Hard Rock Hotel and Emboodhoo Island, also in the same lagoon.
Featured Image: Overwater Villas, Hard Rock Hotel Maldives
Emboodhoo Lagoon was the first fully reclaimed lagoon project, and it was going to be the country’s first integrated resort project and the first lagoon to be leased for tourism. The packages the company undertook collectively comprised of 78 water villas, a walkway jetty, 8 two-storey beach suites, front of House and Back of House buildings, with a value of USD 41.5 million, and a retail and entertainment area, architectural exterior finishes, 24 retail buildings, a dive center, cultural center, marina office, spa, multifunction hall, Hard Rock Café, public toilets and 4 restaurants buildings, which were worth another USD 13.4 million.
The two other projects including the resort were secured whilst the first was ongoing, with the Hard Rock Hotel package commencing in May 2018, and the Retail and Entertainment package beginning in July 2018 respectively. With a tight timeline as the driving force, the company embarked on a momentous journey to perform wonders and complete the projects as per the company’s standards. In the midst of the Crossroads project, AIMA was awarded the COMO Cocoa Island project as well.
Featured Image: The Marina Crossroads, Emboodhoo Lagoon
Maneuvering Through the Obstacle Course
Three projects running concurrently meant the challenges facing the company also multiplied; with the main ones being meeting the tight schedule and finding the required manpower and resources. All three projects needed to be completed within 12 months, therefore, the company had the grueling task of acquiring 2000 plus laborers for the three projects collectively. Additionally, they also required three separate sets of resources, three project teams, and all the associated support services to complete the projects on time. Over 40% of the workforce were recruited locally, however, as a ready supply of 1000 plus people were not available within the Maldives, the company widened its search for a workforce from abroad.
Recruiting the Right Manpower
Determined to ethically outsource laborers, AIMA set out to recruit the necessary numbers through the proper channels, which led to direct negotiations with the Bangladesh embassy in Male’. Upon commencing this discussion, the ambassador personally visited the work site to ensure that the conditions and facilities were adequate, and shortly afterward, AIMA’s HR team traveled to Bangladesh to meet with suitable agents and find the required candidates. Albeit time consuming, their efforts did pay off as they were able to successfully acquire a full flight of workers that duly arrived -taking the workforce numbers to 2000 on the crossroads project alone, and another 1000 were employed across their head office and other small ongoing projects.
Nonetheless, the large workforce required a substantial amount of support services in terms of food, accommodation, and facilities, therefore, temporary worker villages needed to be constructed across the three work sites to house their staff. Moreover, as the 2000 workers were a mix of different nationalities, communication was a daily challenge for the company as the briefings and toolbox sessions had to be conducted in five different languages until the first project neared its completion. Afterward, most of its workforce were redeployed at the marina project, providing a much-needed labor boost as each of the 38 buildings required its own team to ensure the project stayed on target.
Featured Image: AIMA Workers at Emboodhoo Lagoon Contruction Site
Planning and Acquiring Resources
To deliver the packages on time, AIMA’s management spared no expenses in making the necessary purchases in terms of equipment and resources. The timber was brought from a New Zealand timber merchant who was contracted to produce solely for the company, Terracotta tiles for the Marina retail units arrived from Sri Lanka, cement came in from Malaysia and India, the thatched roofs for the villas at The Hard Rock Hotel came from China and Indonesia, and the distinctive arched doors and windows for the marina building were manufactured to order in Malaysia.
The Hard Rock Hotel package also required 2 cranes, which were procured immediately from Singapore and additional excavators, barges, and equipment, were bought, renewed, or updated from reputable suppliers to ensure durability and enable outputs to be met.
Featured Image: Two-storey Beach Suites, Hard Rock Hotel Maldives
For Hard Rock Hotel, Singha had decided to precast the pillars for the water villas in their Singaporean facility, however, the pillar weight meant that only three could be transported in each container, which bumped up the freight charges substantially and added to the logistical challenges and clearance issues. This settled the decision to precast onsite, and it allowed the company to demonstrate their ability in pre-casting, producing the remaining pillars, colonnades for the event hall and other stone structures. In this aspect, the lack of vegetation on the islands worked in AIMA’s favor as the heavy machinery were able to move about without obstruction.
All suppliers needed to provide the resources within the tight timeframe, so the containers arrived consistently to allow continuous productivity. This was not an easy task against the backdrop of the logistical challenges of shipping things to the Maldives, and the inevitable unforeseeable delays caused by rough seas, transshipments, and clearance backlogs. With 20 to 30 containers coming in every month the logistics and clearance teams were fully occupied for weeks, clearing 40 containers a month at the peak of the development.
Featured Image: Hard Rock Hotel Maldives Overwater Villas
Featured Image: Contruction of Hard Rock Hotel Maldives Overwater Villas
Reaching the Finishing Line
The Crossroads project was a milestone for AIMA Construction, catapulting them from a midscale company turning over 20 to 30 million dollars per annum, to a company with a 100 million turnover in the space of 7 months.
The magnitude of these packages gave AIMA a quantum leap in terms of business revenue and with meticulous planning and execution, they were able to overcome every challenge and deliver the project on time -adeptly proving that a local company had the capability and the expertise to compete successfully with international players for multimillion dollar projects. AIMA’s local knowledge and extensive network of local and international partners also served as a powerful advantage, and they have proven that it will continue to be a major asset for all their clients in the upcoming future.
Featured Image: Rock Spa, Hard Rock Hotel Maldives
Featured Image: Gold Beach Villa, Hard Rock Hotel Maldives